Ceramic Foam Filters Manufacturing Process uses polyurethane foam as the carrier. After hydrolysis, the foam is immersed in the coating made of ceramic powder, binder, sintering aid, suspending agent, etc., and then the excess coating is squeezed out, so that the ceramic coating is evenly coated on the framework of the carrier to form a green body, and then the body is dried and roasted by high temperature.
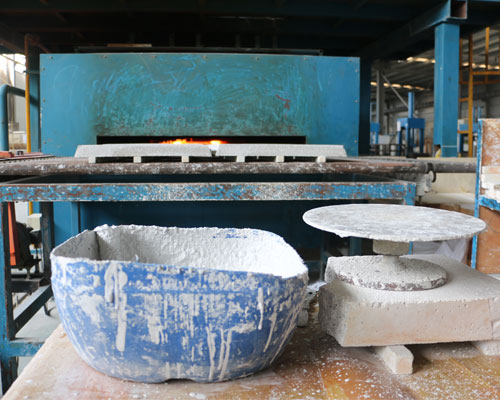
Ceramic Foam Filters Manufacturing Process
The aluminum oxide foam ceramic filter can reduce or eliminate casting defects by mechanical intercepting, rectifying scum and deep adsorption three filtration purification mechanisms, improving the yield and processing performance of the alloy.
In the melting and pouring process of aluminum and its alloy, the defects such as inorganic inclusions and shrinkage pores are the main reasons for casting scrap. Inclusion defects not only affect the appearance of the products, but also seriously reduce the mechanical properties and service life of the products. Therefore, reducing the inorganic inclusions and porosity defects is the key to produce high quality castings.
The traditional alumina foam ceramics are easily eroded and damaged during the long-term contact with aluminum liquid. Although the problem can be solved through early replacement, this will inevitably result in a reduction in the number of single castings, an increase in the number of downtimes, an increase in the cost of production, and a low production efficiency. Moreover, aluminum oxide foam in the contact with aluminum liquid often causes fracture of some holes and Bars due to erosion of molten aluminum, resulting in two fouling. This is extremely unfavorable for some high demanding and high standard products in automobile, aerospace and military industries. Therefore, it is of great significance to improve the corrosion resistance and prolong the service life of alumina foam ceramics.
Ceramic Foam Filters Manufacturing Process
AdTech aluminum oxide foam ceramic filter, which is resistant to aluminum corrosion, has good high temperature stability and corrosion resistance. It can be applied to the production of high quality castings such as automobiles, aerospace and military industries, and prolong the service life of alumina foam ceramics and improve the production efficiency of related enterprises.
The alumina foam ceramic filter is made of polyurethane foam, which is impregnated with ceramic powder and solvent, and is prepared by drying and sintering. It is characterized in that: the ceramic powder is composed of alumina powder, kaolin powder, barium carbonate powder, or barium sulfate powder; the solvent includes water and silica sol. In situ reaction of alumina powder, kaolin powder, barium carbonate powder, or barium sulfate powder with silica in the binder silica sol produces barium feldspar which is not easy to be infiltrated by molten aluminum. A layer of boron nitride coating is applied on the alumina foam ceramic filter.