The degassing of aluminum is based on the principle that dissolved hydrogen gas will move from an area of high concentration (in the melt) to an area of low concentration (in the inert gas). The hydrogen gas disperses in the molten metal as it would if released in a confined space. It will maintain a constant concentration throughout the fusion. Hydrogen gas can migrate through liquid metal almost as quickly as through the air. Therefore, it is not necessary to put every ounce of metal in contact with the inert gas. The efficiency of aluminum degassing is determined by two factors, the rate of transfer through the metal/gas interface and the total surface area available for the transfer.
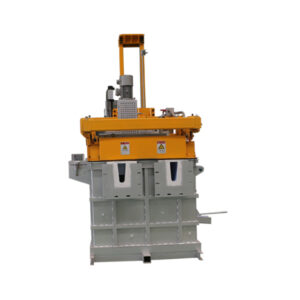
aluminum degassing
When melting scrap aluminum, the process of removing excess hydrogen is essential to producing quality aluminum castings.
Hydrogen is introduced by humidity. Excess hydrogen has a negative effect on the mechanical properties of the finished aluminum by creating porosity and overall shrinkage. It is important to remove excess hydrogen during the melting and casting process.
The introduction of inert gases such as argon or nitrogen into the molten metal can be used to remove hydrogen. As the inert gas bubbles rise through the molten aluminum, the hydrogen diffuses into the inert gas bubbles and essentially disappears. Traditional degassing systems limit mixing, especially at the bottom, where higher speeds are required, resulting in more surface turbulence. The bubbles are larger and the degassing takes longer to achieve the desired results. Melters want superior bubble shear and dispersion, longer bubble retention time in metal, full circulation of molten metal, a non-clogging rotor, and greater thermal shock resistance. In addition, they would prefer to use less inert gas in the process.
AdTech rotary degassing machines use graphite components which are essential for successful metal processing. The rotor head provides increased movement of the metal by throwing the metal outward and pulling the metal out from below for better circulation. The unique rotating motion of the rotor head shears the bubbles to prevent gas from rising. The cleverly designed rotor pushes the metal out and pulls from the bottom to improve flow, increasing the reaction surface area. It operates at a lower speed and eliminates “dead spots” in the melt.
AdTech is an enterprise specializing in the development of new materials and the production of high-precision in-line degassing units since 2012 and has received positive feedback from domestic and overseas markets.