The principle of deep bed filters is what this article wants to describe.
(Only by understanding the principle can you know whether it is suitable)
There are three main types of filters on the market today:
PLATE-TYPE FILTERING UNIT, tubular filter, and deep bed filter.
Ceramic foam filters and tubular filters in continuous casting and rolling production
It has been widely used and achieved remarkable results, but due to the ceramic filter plate
The effect is limited, and currently, it cannot meet the requirements of stable production of double-zero foil blanks, etc.
The need for end products, so continuous casting and rolling production of high-end product billets is mainly
The ceramic filter tube has been hoisted and preheated using ceramic tube filtration technology.
It is easy to crack during the process, and the crack is not easy to be found.
It is difficult to find the inclusions in the cast and rolled products, which brings great difficulties to the subsequent deep processing.
It is a big hidden danger, and it is easy to cause batch waste, the ceramic filter tube technology works
higher cost.
Learn from the deep bed process used in hot rolling and casting large slabs at home and abroad.
filter, to ensure the quality of high-end casting and rolling products, the deep test in continuous casting and rolling
bed filter. The filter medium of the deep bed filter is sintered by a special process
Alumina balls and grit, this depth filtration technology has been used in the foundry field
Recognized to meet the needs of high-end products. There are many in the world
Large aluminum companies: such as Alcoa (Alcoa), Alcan (Alcan),
Novelis has deep bed filter technology. But because of its
Large volume, installation, and replacement of filter media is time-consuming and labor-intensive, more suitable for large batches
The production of a single alloy [1] is difficult to meet the needs of continuous casting and rolling.
Characteristics, of the following problems, are found in the application process of continuous casting and rolling:
① It is difficult to replace alloy grades, and there are many wastes of alloy transfer;
② The heat storage capacity is strong, and it is not easy to adjust the temperature;
③ It isn’t easy to replace the filter medium, and the replacement cycle is long.
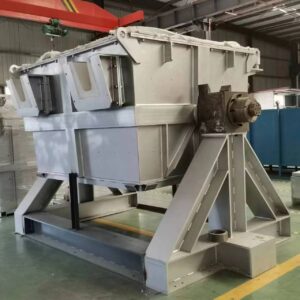
The principle of deep bed filters
Principle of deep bed filter
At present, the filter media of deep bed filters on the market are solid or liquid. According to the characteristics of the molten aluminum used for casting and rolling of the filter medium, the test
Choose alumina balls and grit as filter media. through filter media
The smaller the gap between, the thicker the filter medium, the lower the melt flow rate, and the lower the filtration efficiency.
The better the fruit. The speed at which the filter media captures inclusions is related to the
is proportional to the concentration in the body, that is:
( eN/et) z = KC ( 1 )
In the formula, N – is the amount of slag captured in the filter; Z – is the filter input
depth of mouth; C – concentration of slag inclusions in the melt; t – filtration time; K
– Kinetic parameters, which the following formula can express:
K = K0 ( 1 – N/Nm ) ( 2)
where K0 – kinetic parameter, and melt properties, between filter media
The size of the gap is related to the shape and size of the slag inclusion; Nm – captured by the filter
the maximum amount of slag inclusions.
When N→Nm, K→0, indicating the end of filtration, at this time in the melt
The following formula can express the slag inclusion concentration
C i = C0 exp ( – K0L /um ) ( 3)
In the formula, C I, C0 – the concentration of slag inclusions in the melt before and after filtration; L –
filter media thickness; um – flow rate of the melt in the filter media.
Available filtration efficiency η
η = 1 – C0 /C i = 1 – exp ( – K0L /um ) ( 4)
It can be seen from Equation 4 that the filtration efficiency is related to the thickness of the filter medium and
The flow rate of the melt in the filter medium is closely related, and the thickness of the filter medium is
The larger, the slower the flow rate of the melt in the filter medium, the greater the gap between the filter media.
Small, the higher the filtration efficiency, the better the filtration effect. Principle of deep bed filters [2]
As shown in Figure 1.