Achievement display of aluminum deep processing ceramic foam.
The foam ceramic filter developed by Dongfeng Motor Company has three materials, namely bauxite (Al2O350wt%, SiO235wt%), A2O3 quality (80wt%Al2O3, 20wt%SiO2), and SiC (45wt%siC45wt%Al2O3). The company’s application practice of SiC foam ceramic filter on the ductile iron production line shows that the tensile strength and elongation of ductile iron are increased by 15.3% and 12.5% respectively compared with those without filtration, and the dispersion degree is reduced, and the casting process yield rate Compared with the honeycomb straight-hole ceramic filter, it is 2.8% higher, the casting rejection rate is reduced by about 50%, and the tool life is more than doubled during machining, and good economic and technical benefits have been achieved.
Aluminum deep processing ceramic foam
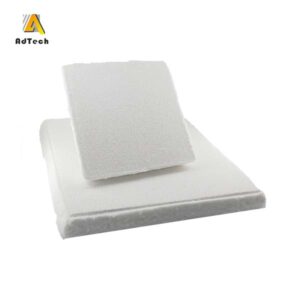
Aluminum deep processing ceramic foam
Nanchang Institute of Aeronautics and Technology has focused on the research of pure magnesium oxide porous ceramic filters for magnesium alloy filtration. Because the standard free enthalpy of formation of magnesium oxide is very low, molten magnesium at high temperatures is very easy to form MgO with some oxides with higher standard free enthalpy of formation, such as SiO2 and Al2O3, which will make the filter with Al2O3 and SiO2 as ceramic base materials. The ceramic framework of MgO rapidly eroded and disappeared, and the reaction products such as MgO entered the magnesium solution and seriously polluted the magnesium solution. Aiming at the characteristics of magnesium alloys, the school successfully developed a high-temperature solid-phase sintered pure magnesium oxide foam ceramic filter. The ceramic framework of this filter itself is not dense, and the apparent porosity is 5~10vol%. This microscopically rough and porous ceramic framework not only easy to adsorbs fine inclusions but also can adsorb flux inclusions in the form of droplets in magnesium solution (MgO and flux are completely wetted). After using a pure MgO foam ceramic filter to purify ZM-5 magnesium alloy liquid, there are no inclusions in the casting, the tensile strength can be increased by 25.2%, and the elongation can be increased by 82%. The magnesium alloy in the gating system can be completely recovered. The aluminum deep processing ceramic foam can surface and skim off when the alloy is remelted. Nanchang Aviation Institute of Technology also uses silicon carbide as the ceramic base material and a small amount of boride as a sintering aid to sinter the foam ceramic filter for cast iron at a lower sintering temperature. Its strength is high, the cost is low, and it can withstand High-temperature molten iron impact for more than 3min. should have the comparative application results of the filter and the high-temperature resistant fiber filter on the ductile iron crankshaft show that the average diameter of the graphite balls is significantly smaller than that of the fiber filter, and the distribution is more uniform.