The Covering Results of flux for aluminum covering agents are applied to the actual production of a recycled aluminum enterprise in Guangdong, and the refining effect is compared with the domestic high-efficiency flux (code-named A) and imported high-efficiency flux (code-named B). The test process is as follows: the regenerated aluminum alloy melt (ADCl2) in the double-chamber melting furnace is respectively transferred into the spoon with a capacity of it, and the amount of aluminum liquid in each experiment is about 6ω0kg, and a series of samples are poured after removing the scum. To characterize the melt quality before refining, then turn on the GBF device (the baffle plate is not inserted into the molten pool), and automatically and quantitatively add the refining flux for aluminum until the liquid level forms a stable vortex. The melt was allowed to stand for 5 and finally, the aluminum slag was removed and collected, and a series of samples were poured to characterize the quality of the melt after refining. In the test, the additional amount of A-type, B-type, and CUI-I-type fluxes was 0.3wt%, 0.2wt%, and 0.15wt% of the aluminum melt, respectively, and the flux for aluminum treatment temperature was set at 740℃.
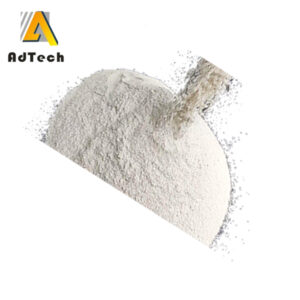
flux for aluminum
The decompressed sample before refining contains more dispersed large-sized pores. After refining with A-type flux for aluminum, the number of pores in the decompressed sample is significantly higher than that in the decompressed sample. The pores are concentrated in the central area of the cross-section: B-type flux and S°CUr- After refining with type I flux, the degassing effect is similar. The size of the pores in the decompressed samples is generally smaller, and the number of pores is significantly reduced in the area near the top of the piece. In addition, the morphology of the upper surface of the decompressed sample was also observed, as shown in the area marked by the red ellipse in Fig. 7. Before refining, the melt contained a lot of gas. The upper surface of the sample was convex after solidification: Type A flux for aluminum was melted after refining. The gas content in the melt is significantly reduced, and the upper surface of the corresponding decompressed sample is approximately flat. For the B-type and SCUT-type fluxes, the gas content of the melt after refining is further reduced compared with the A-type flux, respectively corresponding to the decompression test. The upper surface of the sample is concave only due to solidification shrinkage.