Applied Research on Shotcrete Technology of Alumina Foam Ceramic Filter Plate
1 Prefacee
Foam ceramic is a kind of three-dimensional space grid structure with a high air-void ratio
(80% – 90%) porous ceramics, due to their low density, high strength, and high resistance
Temperature, corrosion resistance, and good filtration and adsorption. Therefore, it is widely applied
It is used in metal melt filtration, automobile exhaust gas treatment, medical materials, and other fields [l-21.
In recent years, through the third-generation filter material – foam ceramic filter
FCF。 That is, the development of CeramicFoamFiher) makes metal-melting products
The qualification rate of the finished products has been dramatically improved, and the product performance has also been greatly improved.
Casting is one of the industries where foam ceramic filters are most widely used
It is to make the disordered and tumbling liquid metal become flat after passing through the foam ceramic honeycomb holes
Stable, uniform, and clean liquid metal. So as to greatly reduce the
The rejection rate of castings caused by casting defects such as materials saves production costs [3].
The shotcrete process is a process in the production of foam ceramics
Generally, there is no such process in the process of ceramic production. Although most domestic foam ceramic manufacturers have adopted the shotcrete process, the foam ceramic field
It is not widely used. There are only a few manufacturers. And the spraying process is not the key
Therefore, there is not much research and understanding of it, and there is no related foam ceramics
Literature report of shotcrete technology.
2 Production process of porous ceramic filter plate
The foam ceramic filter plate is made of polyurethane foam plastic as the carrier
Into the ceramic slurry made of ceramic powder, binder, sintering aid, suspending agent, etc; Then squeeze out the excess slurry to evenly coat the ceramic slurry
The carrier skeleton becomes a green body; Then the green body is dried and sintered at high temperature [4].
This process, also known as the organic foam impregnation method, is a popular foam in China at present
The production process of foam ceramic is the same.
3 Grouting process of foam ceramic filter plate
The uniting process is one of the processes for producing foam ceramic filter plates
The ceramic slurry is atomized and sprayed onto the filter plate through the nozzle under pressure. Its purpose is to improve the surface properties of the green body, including improving the smoothness of the surface and adding
At the same time, thick screen cable also impacts the internal quality of the product. The spraying process is based on the spraying method
The formula mainly includes two forms, manual spraying, and automatic spraying: according to the spraying sequence
It can be divided into spraying after sizing and spraying after drying.
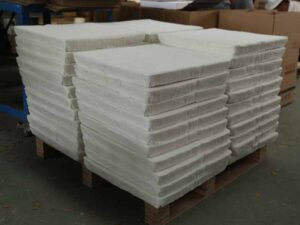
ceramic foam filter