2. Foaming method
The foaming process is adding organic or inorganic chemical substances to ceramic components, generating volatile gas through chemical reactions, etc., and then drying and sintering to make”the porous ceramic filter plate” Compared with the foam impregnation process, the foaming process is easier to control the shape, composition, and density of the product, and can prepare porous ceramic filters with various pore shapes and sizes, especially for the preparation of closed-pore ceramic materials. There are many types of chemical substances used as foaming agents. For example, calcium carbide, calcium hydroxide aluminum powder, aluminum sulfate, and hydrogen peroxide are used as foaming agents; “the porous ceramic filter plate” is prepared by simultaneous foaming of hydrophilic polyurethane plastic and ceramic slurry. ; Mixed with sulfide and sulfate as a foaming agent, etc.
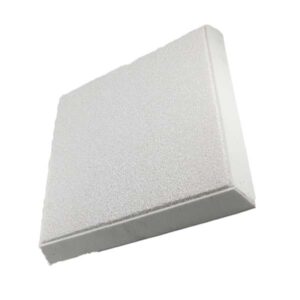
porous ceramic filter plate
3. Add pore former method
This process is to prepare porous ceramic filters by adding a pore-forming agent to the ceramic ingredients, using the pore-forming agent to occupy a certain space in the green body, and then sintering the pore-forming agent to leave the base to form pores. The process flow of preparing the porous ceramic filters by adding a pore-removing agent is similar to the common ceramic process flow. There are two types of pore-forming agents: inorganic and organic. Inorganic pore-forming agents include ammonium carbonate, ammonium bicarbonate, ammonium chloride, and other high-temperature decomposable salts, as well as coal powder, carbon powder, etc. Organic pore formers are mainly natural fibers, high molecular polymers, and organic acids. The shape and size of the pore former particles determine the shape and size of the pores of the porous ceramic material. The molding methods of porous ceramic materials are similar to those of ordinary ceramics, mainly including molding, extrusion, isostatic pressing, rolling, injection and slip casting, etc.
4. Extrusion molding method
There are many forming methods for honeycomb ceramics, and extrusion forming is one of the most commonly used manufacturing methods. Its technological process is raw material synthesis → mixing → extrusion molding → drying → firing → product. In the production process, one of the core processes is extrusion molding, and extrusion molding die is the core technology of extrusion molding. A few days ago, the honeycomb ceramic extrusion molds that have been developed and used in my country reached the specification of 400 holes/in2. The United States and Japan have developed high pore density, ultra-thin-wall honeycomb ceramics with 00 holes/in2 and 900 holes/in2. Our country has also started the research of 600 holes/in2 extrusion die, and achieved initial success.
5. Sol-gel method The sol-gel process mainly utilizes the accumulation of colloidal particles in the gelation process and the small pores left in the process of gel treatment and heat treatment to form a controllable porous structure. Most of these methods produce nano-scale pores, which are mostly used to produce porous ceramic filter plates sol-gel process is a new process for preparing porous ceramic filter plates which are unique compared to other processes. For example, the sol-gel method is used to prepare an alumina porous ceramic filter. Compared with particle mixing, foam impregnation, and spray drying of particles, the sol-gel method can further improve the control of pore size distribution, phase transition, and purity of alumina in the porous ceramic filter plate and microstructure. The table compares the characteristics of the above four process methods.