In the late 1970s, the United States developed a sponge-like ceramic foam filter (CFF) made of materials such as alumina and chromium oxide. The ceramic filter is not only good in purification technology, but also easy to use. The initial pressure difference of the melt passing only needs 100~150mm, and once passed, it only needs to maintain the pressure difference of 2~10mm. The principle of foam ceramic filtration and purification is the same as that of ceramic tube filtration, which belongs to the deep filtration mechanism and has a higher porosity (80%~90%) than ceramic tubes. Therefore, it has a large flow capacity and is suitable for filtration and purification in continuous casting and continuous rolling production. Filtering with ceramic foam filter plate is currently the most effective method for removing inclusions in the aluminum melt.
In recent years, some new technologies for purifying aluminum liquid at home and abroad have also been studied, such as vacuum dynamic processing, ultrasonic continuous degassing purification and corundum ceramic filters, which have received good results, but these process methods are more complicated and costly It is difficult to promote in large numbers in the industry. Metal filters and fiber cloth filters used by low-end customers can only remove large inclusions in the aluminum alloy melt, but cannot remove inclusions below the micron level, and the metal filters will also contaminate the aluminum alloy. The use of foam ceramic filter plate can filter out small inclusions, significantly improve the mechanical properties and appearance quality of the product.
Advantages of Foam Ceramic Filter Plate
Because the filter plate filters out small inclusions, the number of effective crystal nuclei in the aluminum liquid is reduced. As a result, the liquid nuclei grow under a large supercooling condition, the solidification time is shortened, and the structure is refined; the hydrogen content in the aluminum liquid is reduced. Hydrogen atoms can be adsorbed on some oxidized inclusions, and the oxidized inclusions can become the core of the bubble growth, so the inclusions are filtered out and the gas on them is also removed. Through adsorption, the content of harmful elements (sodium and potassium) in the aluminum liquid can be removed. According to different customer requirements or on-site environmental conditions, selecting a filter plate suitable for ensuring product quality can effectively control slag inclusions.
The slag removal outside the furnace is mainly completed by a ceramic filter plate, which has a multi-layer network, multi-dimensional through holes, and the holes communicate with each other. During filtration, the aluminum liquid carries the inclusions along the tortuous channels and pores, and is directly intercepted, adsorbed, and deposited when it contacts the foamed skeleton of the filter plate. When the melt flows in the holes, the filter plate channel is curved. The melt flowing through the channel changes the direction of flow, and the inclusions in it collide with the anvil of the hole wall and firmly adhere to the hole wall.
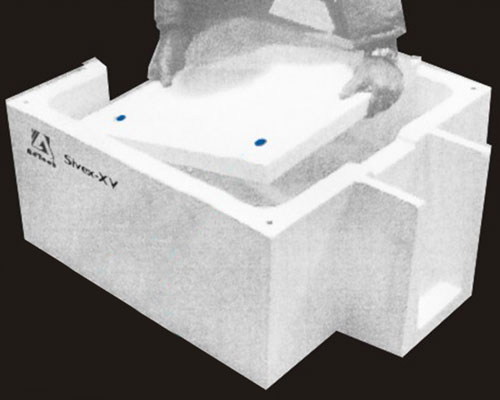
Ceramic Foam Filters for Casting
Use of CFF Filter Plate
The foam ceramic filter plate is installed in the filter box between the furnace port and the diverter plate. The closer the filter box is to the diverter plate, the better. The reason is that it can shorten the flow distance of aluminum liquid after filtration, thereby reducing or avoiding the re-generation of oxides. The aluminum liquid flows out from the furnace mouth through the filter box, and then flows into the distribution plate through the flow groove. When the filter device is started, the drop before and after the melt filtration is about 30 mm. With the extension of the filtration time, the inclusions on the surface of the filter plate and the wall of the hole increase, the filtration flow rate decreases, and the front and rear drop increases, and the drop increases to 50~100mm by the end of casting.
The filtering effect of the filter plate is mainly guaranteed by its size and porosity. The larger the porosity of the filter plate, the worse the slag removal effect. For the very strict aluminum products, the filter plate with small porosity should be selected. The filtration efficiency increases with the increase of the particle size and the thickness of the filter layer, and decreases with the decrease of the filter pore size and the flow rate of the aluminum liquid.