Ceramic Foam Filter Suppliers have developed foam ceramics as a new type of ceramic filter material for many years. Generally, a filter plate with a thickness of 50mm and a length of 200~600mm is made, and the porosity is 0.8-0.9.
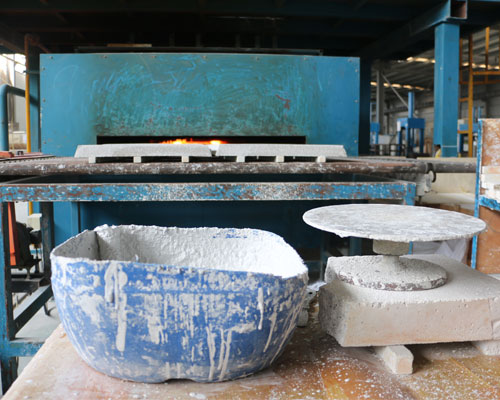
Ceramic Foam Filter Suppliers
When the foam ceramic filter is filtering the aluminum liquid, the aluminum liquid flows through the tortuous holes of the ceramic, and the inclusion particles contained in it are retained in the ceramic plate due to the combined effect of the axial pressure, friction, and surface adsorption force of the aluminum liquid flow. The inner surface of the hole and the crevice cave, so that the inclusion particles and the aluminum liquid are separated.
The slag remaining on the ceramic foam filter after a period of time also participates in the adsorption and retention of the slag. Its ability to adsorb and trap molten aluminum is much greater than that of the ceramic plate, making it possible for the ceramic filter plate to filter out much smaller slag than its own perforation. Generally speaking, the thicker the ceramic plate, the smaller the eye, and the aluminum liquid passes through the ceramic plate. The slower the flow rate, the better the filtering effect.
The total amount and cleanliness of molten aluminum not only affect the filtering effect, but also affect the service life of the ceramic plate. Usually, the filter device with foam ceramic plate is similar to the glass cloth filter, and it is directly placed on the distribution plate. Before casting, the ceramic plate should be preheated to about 600 degrees. Because the ceramic plate is hard and brittle and has poor thermal conductivity, the initial addition should be slow. When preheated to above 200 degrees, the heating speed can be increased, otherwise, the ceramic plate is easily broken.
The current level of the aluminum foil product quality is also a reflection of the quality level of cast-rolled aluminum melt. In order to make the product high-quality and produce high-quality aluminum foil, there are certain defects in the purification process, equipment and management, which are mainly reflected in the following aspects:
Metal transfer: The metal transfer drop from the smelting furnace to the static furnace is large, and the slagging and gas suction are serious.
Flow supply system: The heat preservation of the degassing box and the launder is not ideal, and the melt temperature is controlled too high or the melt temperature is controlled too low. It occurs when the temperature of the melt is controlled too low, resulting in the burning of the launder and the increase of hydrogen absorption and metal oxidation.
Both in-furnace (stationary furnace) degassing and online degassing use a single inert gas-argon. The inert gas does not react with aluminum at the general melting temperature. Because the blown bubbles are large, the floating speed is fast , The hydrogen in the bubbles rises to the surface without reaching equilibrium, and the degassing effect is not ideal.
Filtration: The Ceramic Foam Filter Suppliers offer ceramic filters with an accuracy of 30~50ppi. Because the size of the filter box cavity is difficult to maintain the original size after a period of use, and the filter has the phenomenon of slag drop, it is suitable for the production of high-quality aluminum foil In other words, its filtration accuracy is not easy to achieve, and its stability is also poor.