Filtration is the most effective and reliable method to remove non-metallic inclusions in the aluminum melt. There are several filtering methods, the best result is Metal Foam Filter.
Metal Foam Filter is widely used worldwide due to its convenience, good filtering efficiency and low price. In developed countries, 50% of aluminum alloy melts are filtered by foam ceramic filter plates. In order to meet the requirements of high-quality products for melt quality, the pore size of the ceramic foam filter is getting smaller and smaller.
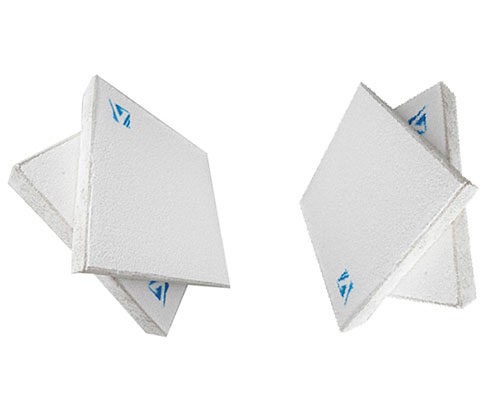
Metal Foam Filter
Metal Foam Filter Manufacturing Process
The uniqueness of the organic foam impregnation process is that it relies on the open-cell 3d network framework of organic foam with a special structure to prepare a good slurry, uniformly coat it into a network in an organic form, and burn it after obtaining the network porosity Drop organic bubbles. The pore size of the final product is mainly determined by the pore size of the organic foam, and the thickness of the organic foam is also related to the thickness of the coating. However, the porous body structure of the pore mesh is almost the same as the structure of the organic foam matrix, that is, the naked eye 3d mesh skeleton structure.
This special structure makes it a filter material with significant advantages:
- Through fluid, the pressure loss is small.
- The surface area and efficiency of fluid contact are high.
- Light weight. Porous ceramics are specially used for fluid filtration in molten metal filters. Compared with sintered bodies and glass fiber cloth, the operation is simple, which not only saves energy, reduces costs, but also has higher filtration efficiency.
The organic foam for preparing mesh porous ceramic materials must meet the following conditions:
(1) It must be a mesh material to ensure its free penetration, and the ceramic slurry can adhere to each other, thereby forming a three-dimensional framework network during firing.
(2) Ceramic slurry must have a certain degree of hydrophilicity and strong adsorption.
(3) It should have sufficient elasticity to ensure that the excess slurry can be quickly squeezed out after rebounding and restore its shape.
(4) It volatilizes below the ceramic sintering temperature and does not pollute the ceramic.