The purification method of aluminum alloy can be divided into adsorption purification and non-adsorption purification. Adsorption purification refers to the direct contact between the aluminum melt and the adsorbent, so that the Aluminum Casting Foundry Flux and the solid inclusions and gas in the melt undergo physical and chemical reactions to achieve the purpose of degassing and impurity removal.
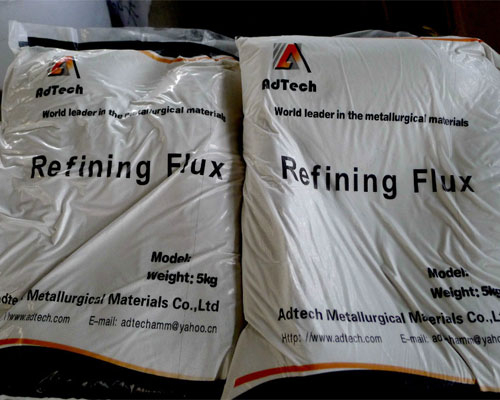
Aluminum Casting Foundry Flux
Aluminum Casting Foundry Flux
The flux method is to add Aluminum Casting Foundry Flux to the melt through a series of physical and chemical actions during the melting of aluminum alloy to achieve the purpose of degassing and removing impurities. The impurity removal ability of the flux depends on the adsorption and dissolution of oxide inclusions and the chemical interaction between the flux and the melt. The smaller the interfacial tension between the flux and the inclusions, the better the adsorption of the flux and the stronger the impurity removal effect.
In addition to Aluminum Flux, which are mainly used to remove gases and impurities, there are other fluxes, such as covering agents and slag cleaners. The repeated use of various fluxes will increase smelting costs and increase the possibility of artificial introduction of impurities. Therefore, the development of a new type of flux with multiple functions is still one of the future development directions. At present, there are many types of fluxes developed and used at home and abroad, such as those produced by AdTech.
At room temperature, most fluxes are solid or gas, and some are liquid, such as CCl4. The advantages of solid flux are small size, easy to transport and store, but strong moisture absorption, so it must be sealed.
In order to improve the purification effect of solid flux, the flux can be compressed into small pieces, wrapped in aluminum foil, placed in a long-handled drilling container, and inserted into the bottom of the molten pool.
For flux based on NaCl and KCl mixed salt, the mixed salt can be melted in proportion, and then refractory ingredients (such as Na3AlF6) are added to the sealed iron box after stirring and cooling.
Before use, the flux should be stored in a high temperature and dry place, such as a place near the furnace, to prevent moisture. The use of covering flux in the furnace can reduce melting consumption and prevent the molten aluminum from absorbing gases in the furnace.
However, the consumption of the covering flux is high, which increases the production cost, and is usually not used in small and medium-sized aluminum processing plants.
Cleaning flux is usually used to spread the mixed powder flux on the surface of the molten pool after the aluminum material is melted, and then use a long-handled tool to stir the molten aluminum to float the ashes.
During the stirring process, some flux is added to the molten pool and reacts with the molten aluminum to form a gaseous substance insoluble in aluminum, which plays a role of degassing and ash removal during the rise of bubbles.