“The aluminum extraction process“.
Since the advent of the foam ceramic filter plate technology in the 1970s, it has shown great vitality in producing aluminum and aluminum alloy materials. With the development of society, the quality requirements of aluminum products are getting higher and higher, and the application of ceramic filter plates will become more and more extensive. In recent years, the quality of domestic ceramic filter plates has been greatly improved, but due to the backward production technology and equipment, the quality of filter plates still cannot meet the needs of production, and the filter plates used by some aluminum processing enterprises are still imported from abroad. Since FOSECO entered the Chinese market as a joint venture with Shenzhen Jinke Special Materials Co., Ltd. in the early 1990s, the production line built with British advanced equipment, raw materials, and production processes was officially put into operation in early 1997. After years of hard work, the production of raw materials has been localized, the quality of the produced filter plates has reached the technical indicators of FOSECO, and the products have been sold to foreign countries and Hong Kong and Taiwan regions. This article combines the existing production technology of ceramic filter plates. An overview of the main aspects
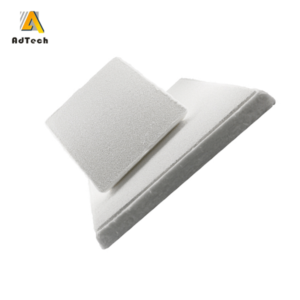
aluminum extraction process
- Requirements of filter plate for raw materials
The ceramic filter plate is made of continuous reticulated foam plastic as the skeleton, impregnated with mud, and fired at high temperatures, so the raw materials for making the porous ceramic filter are divided into foam and mud. 1.1 Foam
“The aluminum extraction process ”
The foam used in the production of filter plates should have sufficient elasticity and strength to ensure recoverability and non-breakage when immersed in mud. It will not cause local depressions, cracks, etc. during the immersion stage. The current problems of domestic foam: First, the strength is not enough, it cannot carry enough mud during extrusion, and it is easy to tear during extrusion; second, the elasticity is small, the recovery is poor, and the foam is deformed greatly after immersion, usually describing the foam specifications. The parameter is PPI (pores per inch, that is, the number of pores per inch length). PPI does not reflect the size of the foam pores. Some foreigners suggest that CPI (cells per inch, see Figure I) be used instead. People still use PPI. In practice, people can’t accurately measure the PPI or CPI of foam. The traditional method of measuring the number of pores with a straight line method is very inaccurate. At present, FOSECO uses the method of measuring the air permeability of the foam to determine the specifications of the foam, that is, under the condition of a certain airflow, measure the air pressure drop before and after passing through the foam, and then convert the value of the air pressure drop into the traditional representation method PPL traditional measurement. The method is a sensory measurement, which cannot reflect the influence of blind pores in foam on the foam, but this method can reflect the real “number of pores” of the foam, which has a certain scientific nature, and the results can accurately reflect the specifications of the foam (see Figure 2)