Ceramic foam filter for aluminum can be used in various casting alloys, and the product has been commercialized. This kind of filtration process has been widely promoted in industrially developed countries, and it has become the simplest and most effective method to improve the mechanical properties of castings and reduce pores and inclusions.
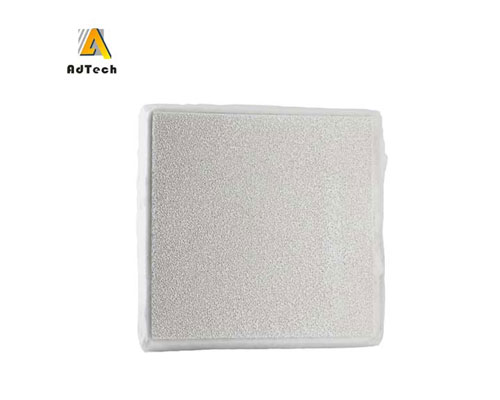
Ceramic Foam Filter for Aluminum
The following is the use effect of ceramic foam filter for aluminum.
Saving metal
In order to reduce inclusions during the pouring process, efforts are often made in the pouring system to try to make the inclusions in the molten metal stay in the pouring system before entering the cavity. If there are serious inclusions in the castings, every effort should be made to increase the height and length of the runner and increase the volume of the slag bag, thus reducing the production rate of the casting process.
Reduce machining allowance and improve cutting performance
In the process design, the non-processed surface of the casting is often poured upward, because there are often inclusions on the upper part of the mold, and the inclusions are not easy to be noticed when they remain on the non-processed surface. If it has to be poured with the processing surface facing up, the processing allowance on this surface is also left particularly large.
Improved metal recovery rate
The fluidity of the molten aluminum is improved. After the molten aluminum is filtered, the non-metallic inclusions are reduced, and the turning of the molten metal during the filtration greatly reduces the gas content, which reduces the viscosity of the molten aluminum, reduces the effective crystal nucleus, and the molten aluminum is too cold. It can nucleate and crystallize at low temperature, which increases the crystallization speed and shortens the solidification time by 10-25%, which is equivalent to prolonging the retention time of molten aluminum, thereby improving the filling ability of molten aluminum.
Reduced casting scrap rate
The engine cylinder head is an important casting with complex structure and thin wall, which requires sealing, so the pouring temperature is higher than that of ordinary castings, and the inclusions are not easy to accumulate under the same conditions. In the past, although many slag-retaining measures were designed in the gating system, such as closed, flow blocking devices, etc., the waste rate of slag, sand, and holes remained high at around 12%. After the filter is used, the pouring time is stable, the leakage phenomenon is significantly reduced, and the waste rate of slag, sand, holes, etc. has stabilized below 3% in the past few years.
Improved mechanical properties of castings
Non-metallic inclusions destroy the continuity of the metal matrix and produce stress concentration at the edges of the inclusions, thereby reducing the mechanical properties. The inclusions distributed on the grain boundaries are prone to intergranular fracture.
The use of ceramic foam filter can filter out the inclusions less than 1-2um in the molten metal, and also remove the gas in the molten metal, improve the purity of the metal, and improve the physical and mechanical properties.
Simplify the pouring system and improve the utilization rate
In the production of spheroidal aluminum castings, when spheroidizing agent or inoculant is added, due to poor particle control, or extremely uneven composition, or when the temperature of aluminum water is low, segregation is easy to occur. In the past, a closed gating system was generally used to increase the height ratio between the runner and the inner runner, and the method of lengthening and enlarging the runner was used to solve the problem of unmelted particles “Freeze” in the gating system.
The use of a filter can filter out scattered and fine slag particles without having to consider the design of a complex structure. The pouring system can be greatly simplified, so that the area of the pouring system on the template can be greatly reduced, which is advantageous for the layout of the template, and originally only 4 appearances can be placed You can put 1-2 more. The yield rate and process yield rate of castings can also be improved.