The area of metal passing through the Filter Foundry should be large enough to prevent the casting speed and pouring time affected by the installation of the filter. Therefore, the factors of slag collection, filter and damping should be considered in the process. Therefore, the ratio of the cross-section area of the filter to the normal runner area is 2.5-4.0:1.
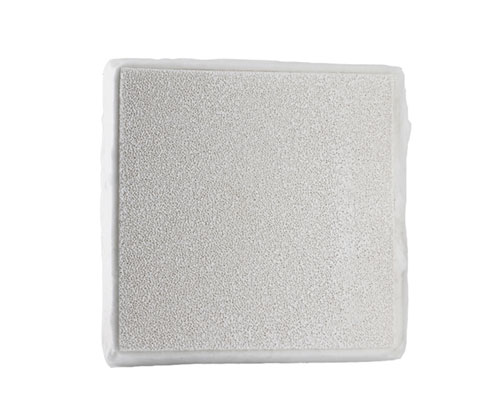
Filter Foundry
There should be enough space before and after the filter, which is beneficial to the collection of inclusions and the smooth flow of molten metal. Using foam ceramic filter to prevent filtration inclusions from affecting metal circulation, filter size is selected according to the filtration volume of metal liquid.
If the aluminum water in the whole box is too much or too dirty, the runner can be bifurcated and multiple filters can be used.
If the ceramic filter media is not used properly, the effect is worse than other filters.
Filter Foundry
The design of the system should ensure that all the aluminum alloy liquid passes through the filter (if part of it fails to pass, the aluminum liquid will be impure, and turbulent flow will be generated, and slag will be formed by entraining air).
The filter area of the filter should be large enough to not affect the flow rate of aluminum alloy liquid (the minimum flow rate should be located at the minimum section of the sprue).
There should be enough space before and after the filter to collect inclusions.
Aluminum alloy liquid should be melted in melting furnace (avoid oxidation and slag removal treatment) and refining slag removal and degassing in holding furnace. Because the filtration capacity of the filter is limited, the aluminum alloy liquid that is too dirty will cause the aluminum alloy liquid filtered last to be dirtier than the aluminum alloy liquid filtered first.