Aluminum water porous ceramic filter product application:
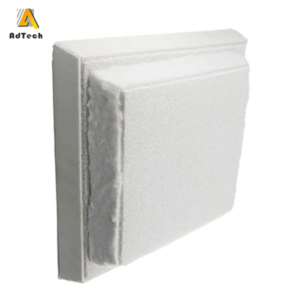
porous ceramic filter
The aluminum-water porous ceramic filter adopts a three-dimensional network structure and an organic foam body connected to pores as a carrier, and invades it into a thixotropic alumina material slurry, and adopts a square correction center distance automatic extrusion process to make the slurry uniform It is coated on the foam body skeleton of the carrier, and is baked at a high temperature of 1180°C after drying and curing. Installed in the filter box for filtering impurities in aluminum alloy liquid, meeting the production of high value-added, high-tech performance aluminum alloy precision castings such as aviation and transportation. Such as computer hard disks, PS substrates for printing, canning materials, jet turbine engine fan blades, and other products.
Product advantages of aluminum water metal foam filter:
1. Adopt the principle of adsorption to filter, which can effectively remove large inclusions in molten aluminum and effectively absorb small inclusions of small size;
2. No slag falling, effectively reducing the pollution of molten aluminum;
3. Good thermal shock resistance improved corrosion resistance to molten metal;
4. Automatic assembly line production, three calibration procedures, accurate size, more suitable for filter box;
5. Improve surface quality, improve product performance, and improve microstructure.
Instructions for use of aluminum water porous ceramic filter:
1. Check and clean the debris on the surface of the filter box, and keep the filter box clean and undamaged.
2. Gently put the filter plate into the filter box, and press the sealing gasket around the filter plate tightly by hand to prevent the molten aluminum from flowing or floating. Evenly preheat the filter box and filter plate to make it close to the temperature of the aluminum liquid, and the preheating temperature of the filter plate should not be lower than 260°C. Preheating to remove adsorbed water is beneficial to help the initial filter pore size to open instantly, preventing thermal expansion and contraction from causing partial pore blockage of the filter plate. Electric or gas heating can be used for preheating, and normal heating takes 15-30 minutes.
4. Pay attention to observing the change of the aluminum hydraulic head during casting, and maintain the flow control of the normally demanded aluminum liquid. The normal initial pressure head is 100-150mm. When the aluminum liquid starts to pass through, the pressure head will drop below 75-100mm, and then the pressure head will increase slowly.
5. During the normal filtration process, avoid knocking and vibrating the filter plate. At the same time, the launder should be filled with molten aluminum to avoid the disturbance of too large or too small molten aluminum.
6. After filtering, take out the filter plate in time and clean the filter box.