Preparations before the use of cartridge filter
cartridge filtration principle:
The molten aluminum entering the cartridge filter equipment contains Various impurities and large particles are filtered out by the surface media of the filter tube, while small particles are filtered out by The media inside the filter tube is adsorbed, and pass through the double filtering effect of the filter tube.
Finally, the high-quality molten metal that meets production requirements is obtained.
Equipment composition:
(1) Intermediate electrical box; (2) Heating component; (3) Box cover; (4) Box body; (5) Pipe group and lifting fixture; (6) Wedge block;
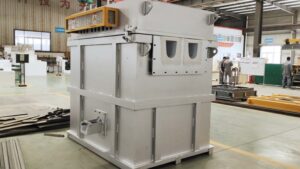
Cartridge filter
Preparation before official operation
1 Install the tap out cone onto the conical plug connector and secure it. please put them in the refractory
material lining; lower the locking arm into position. Compressed ceramic fiber cone, obtained by tightening the provided locking bolts
Liquid metal tight seal.
2 Check whether the parameter settings of the operation interface are correct.
Equipment baking
1 Purpose of baking:
Eliminate the adsorbed water of the insulation layer and fixed lining castables and reduce the thermal stress of the lining materials.
2 Operation requirements and precautions:
a. You can put a small amount of carbon at the bottom of the box, and the height of the carbon layer should not exceed 50mm. Close the upper cover of the filter box.
Use insulation cotton to densely block the inlet and outlet of the filter box;
b. Before baking, twist off the vent nuts around the box to facilitate the drainage of moisture from the insulation lining;c. The upper opening of the box should be covered with a 20mm thick fiber blanket and the box cover should be well sealed. The aluminum inlet and outlet of the box should be well sealed. Use a fiber blanket to plug it tightly, but leave a moisture discharge hole of appropriate size before 400℃, and plug it tightly after 400℃.
d. Insert the thermocouple into the temperature measuring hole in the box cover and extend it to the middle and lower part of the cavity to control the temperature of the furnace gas. It is best to place the thermocouple in the drain hole.
Insert a thermocouple and a digital thermometer to monitor the temperature difference between the upper and lower furnaces.
e. The normal process temperature of the aluminum liquid in the box is about 750℃, and the furnace gas conduction temperature difference is about 50℃, so the temperature during the maximum control temperature of furnace gas is 800℃.
f. If the temperature control meter is equipped with a program control function, it will automatically run according to the baking curve setting program but can also be controlled manually.
g. If the temperature control meter does not have a program control function, time-stepped manual control is adopted. The most powerful power regulator
The maximum current does not exceed the rated current.
h. After the heat preservation at 800℃ is completed, aluminum production can be started. If it is not put into production, the temperature must be lowered to 100℃ before opening the lid for inspection. Otherwise, there is a risk of cracking of the lining; or the lid must not be opened until room temperature. Don’t open the lid halfway.